అనిలాక్స్ రోలర్ల వాడకంలో అనిలాక్స్ రోలర్ కణాల నిరోధం వాస్తవానికి అత్యంత అనివార్యమైన అంశం,దీని వ్యక్తీకరణలు రెండు కేసులుగా విభజించబడ్డాయి: అనిలాక్స్ రోలర్ యొక్క ఉపరితల నిరోధం (చిత్రం.1) మరియు అనిలాక్స్ రోలర్ కణాల ప్రతిష్టంభన (చిత్రం. 2).
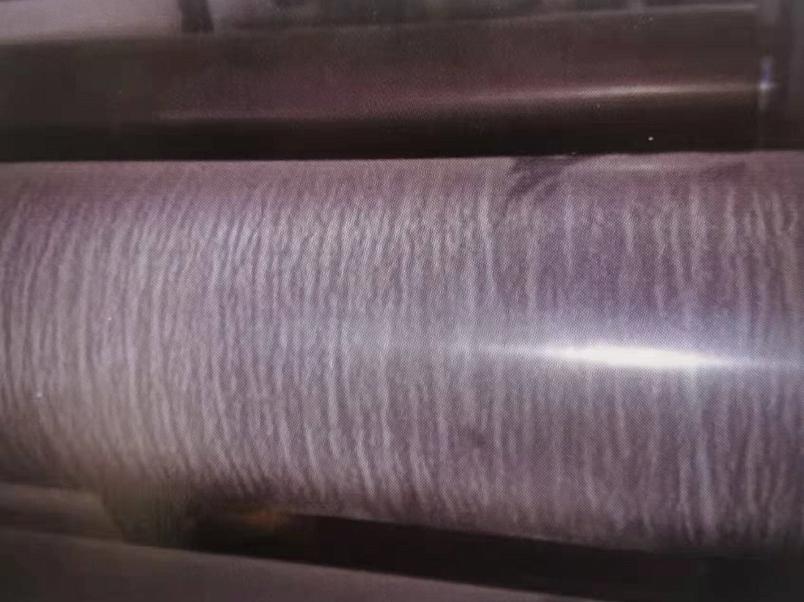
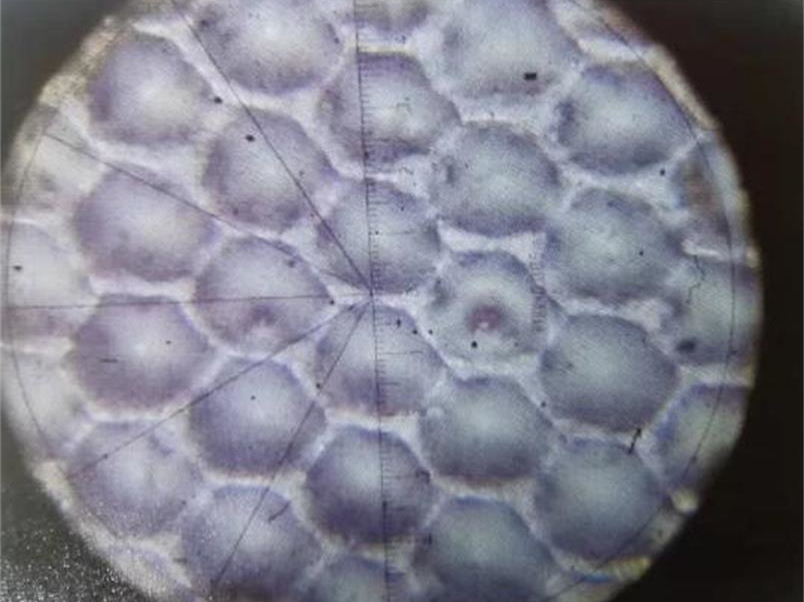
చిత్రం .1
చిత్రం .2
ఒక సాధారణ ఫ్లెక్సో ఇంక్ వ్యవస్థలో ఇంక్ చాంబర్ (క్లోజ్డ్ ఇంక్ ఫీడ్ సిస్టమ్), అనిలాక్స్ రోలర్, ప్లేట్ సిలిండర్ మరియు సబ్స్ట్రేట్ ఉంటాయి. అధిక-నాణ్యత ప్రింట్లను పొందడానికి ఇంక్ చాంబర్, అనిలాక్స్ రోలర్ సెల్స్, ప్రింటింగ్ ప్లేట్ చుక్కల ఉపరితలం మరియు సబ్స్ట్రేట్ ఉపరితలం మధ్య స్థిరమైన ఇంక్ బదిలీ ప్రక్రియను ఏర్పాటు చేయడం అవసరం. ఈ ఇంక్ బదిలీ మార్గంలో, అనిలాక్స్ రోల్ నుండి ప్లేట్ ఉపరితలానికి ఇంక్ బదిలీ రేటు సుమారు 40%, ప్లేట్ నుండి సబ్స్ట్రేట్కు ఇంక్ బదిలీ దాదాపు 50%, అటువంటి ఇంక్ పాత్ బదిలీ అనేది సాధారణ భౌతిక బదిలీ కాదని, ఇంక్ బదిలీ, ఇంక్ ఎండబెట్టడం మరియు ఇంక్ పునఃసాల్వింగ్తో సహా సంక్లిష్టమైన ప్రక్రియ అని చూడవచ్చు; ఫ్లెక్సో ప్రింటింగ్ మెషిన్ యొక్క ప్రింటింగ్ వేగం వేగంగా మరియు వేగంగా పెరుగుతున్నందున, ఈ సంక్లిష్ట ప్రక్రియ మరింత క్లిష్టంగా మారడమే కాకుండా, ఇంక్ పాత్ ట్రాన్స్మిషన్లో హెచ్చుతగ్గుల ఫ్రీక్వెన్సీ కూడా వేగంగా మరియు వేగంగా మారుతుంది; రంధ్రాల భౌతిక లక్షణాల అవసరాలు కూడా పెరుగుతున్నాయి.
క్రాస్-లింకింగ్ మెకానిజం కలిగిన పాలిమర్లను సిరా పొర యొక్క సంశ్లేషణ, రాపిడి నిరోధకత, నీటి నిరోధకత మరియు రసాయన నిరోధకతను మెరుగుపరచడానికి పాలియురేతేన్, యాక్రిలిక్ రెసిన్ మొదలైన సిరాల్లో విస్తృతంగా ఉపయోగిస్తారు. అనిలాక్స్ రోలర్ కణాలలో సిరా బదిలీ రేటు కేవలం 40% మాత్రమే కాబట్టి, అంటే, కణాలలోని చాలా సిరా వాస్తవానికి మొత్తం ముద్రణ ప్రక్రియలో కణాల దిగువన ఉంటుంది. సిరాలో కొంత భాగాన్ని భర్తీ చేసినప్పటికీ, కణాలలో సిరాను పూర్తి చేయడం సులభం. రెసిన్ క్రాస్-లింకింగ్ సబ్స్ట్రేట్ యొక్క ఉపరితలంపై జరుగుతుంది, ఇది అనిలాక్స్ రోల్ యొక్క కణాల ప్రతిష్టంభనకు దారితీస్తుంది.
అనిలాక్స్ రోలర్ యొక్క ఉపరితలం బ్లాక్ చేయబడిందని అర్థం చేసుకోవడం సులభం. సాధారణంగా, అనిలాక్స్ రోలర్ను సరిగ్గా ఉపయోగించరు, తద్వారా సిరా క్యూర్ చేయబడి అనిలాక్స్ రోలర్ ఉపరితలంపై క్రాస్-లింక్ చేయబడుతుంది, ఫలితంగా అడ్డంకులు ఏర్పడతాయి.
అనిలాక్స్ రోల్ తయారీదారుల కోసం, సిరామిక్ పూత సాంకేతికత పరిశోధన మరియు అభివృద్ధి, లేజర్ అప్లికేషన్ సాంకేతికత మెరుగుదల మరియు అనిలాక్స్ రోల్స్ చెక్కిన తర్వాత సిరామిక్ ఉపరితల చికిత్స సాంకేతికత మెరుగుదల అనిలాక్స్ రోల్ కణాల అడ్డుపడటాన్ని తగ్గించగలవు. ప్రస్తుతం, సాధారణంగా ఉపయోగించే పద్ధతులు మెష్ గోడ యొక్క వెడల్పును తగ్గించడం, మెష్ లోపలి గోడ యొక్క సున్నితత్వాన్ని మెరుగుపరచడం మరియు సిరామిక్ పూత యొక్క కాంపాక్ట్నెస్ను మెరుగుపరచడం. .
ప్రింటింగ్ ఎంటర్ప్రైజెస్ కోసం, అనిలాక్స్ రోలర్ కణాల అడ్డంకిని తగ్గించడానికి సిరా ఎండబెట్టే వేగం, ద్రావణీయత మరియు స్క్వీజీ పాయింట్ నుండి ప్రింటింగ్ పాయింట్కు దూరాన్ని కూడా సర్దుబాటు చేయవచ్చు.
తుప్పు పట్టడం
తుప్పు అనేది అనిలాక్స్ రోలర్ ఉపరితలంపై పాయింట్ లాంటి ప్రోట్రూషన్ల దృగ్విషయాన్ని సూచిస్తుంది, ఇది చిత్రం 3లో చూపబడింది. క్లీనింగ్ ఏజెంట్ సిరామిక్ గ్యాప్ వెంట దిగువ పొరలోకి చొరబడి, దిగువ మెటల్ బేస్ రోలర్ను తుప్పు పట్టించి, లోపలి నుండి సిరామిక్ పొరను విచ్ఛిన్నం చేసి, అనిలాక్స్ రోలర్కు నష్టం కలిగించడం వల్ల తుప్పు ఏర్పడుతుంది (చిత్రం 4, చిత్రం 5).
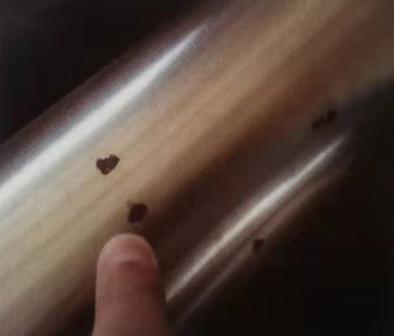
చిత్రం 3
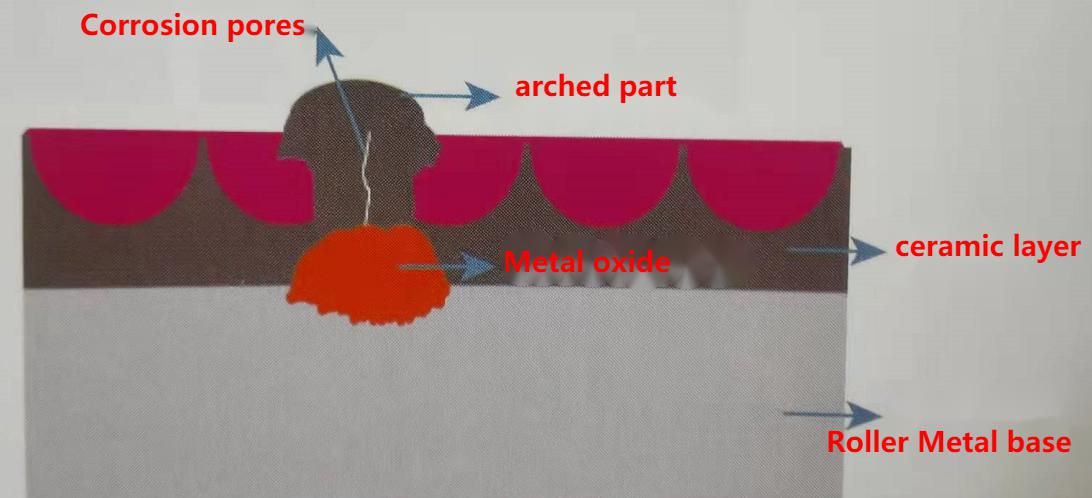
చిత్రం 4
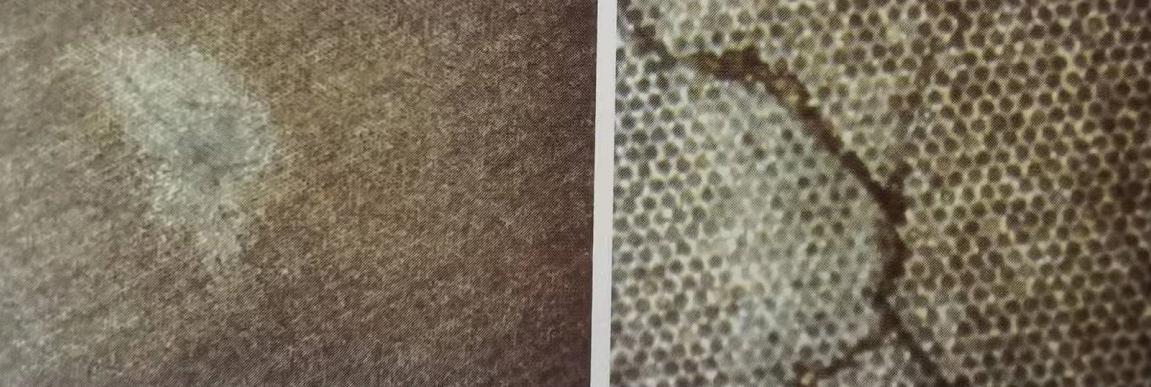
సూక్ష్మదర్శిని క్రింద మూర్తి 5 తుప్పు
తుప్పు ఏర్పడటానికి కారణాలు క్రింది విధంగా ఉన్నాయి:
① పూత యొక్క రంధ్రాలు పెద్దవిగా ఉంటాయి మరియు ద్రవం రంధ్రాల ద్వారా బేస్ రోలర్ను చేరుకోగలదు, దీని వలన బేస్ రోలర్ తుప్పు పట్టుతుంది.
② బలమైన ఆమ్లాలు మరియు బలమైన క్షారాలు వంటి శుభ్రపరిచే ఏజెంట్లను దీర్ఘకాలికంగా ఉపయోగించడం, ఉపయోగం తర్వాత సకాలంలో స్నానం చేయడం మరియు గాలిలో ఆరబెట్టడం అవసరం లేదు.
③ శుభ్రపరిచే పద్ధతి తప్పు, ముఖ్యంగా పరికరాలను ఎక్కువసేపు శుభ్రపరిచేటప్పుడు.
④ నిల్వ పద్ధతి తప్పు, మరియు ఇది చాలా కాలం పాటు తేమతో కూడిన వాతావరణంలో నిల్వ చేయబడుతుంది.
⑤ సిరా లేదా సంకలనాల pH విలువ చాలా ఎక్కువగా ఉంటుంది, ముఖ్యంగా నీటి ఆధారిత సిరా.
⑥ ఇన్స్టాలేషన్ మరియు వేరుచేయడం ప్రక్రియలో అనిలాక్స్ రోలర్ ప్రభావితమవుతుంది, ఫలితంగా సిరామిక్ పొర అంతరం మారుతుంది.
తుప్పు ప్రారంభానికి మరియు అనిలాక్స్ రోల్కు చివరికి నష్టం జరగడానికి మధ్య ఎక్కువ సమయం ఉన్నందున ప్రారంభ ఆపరేషన్ తరచుగా విస్మరించబడుతుంది. అందువల్ల, సిరామిక్ అనిలాక్స్ రోలర్ యొక్క బ్యాగింగ్ దృగ్విషయాన్ని కనుగొన్న తర్వాత, ఆర్చ్ యొక్క కారణాన్ని పరిశోధించడానికి మీరు సిరామిక్ అనిలాక్స్ రోలర్ సరఫరాదారుని సకాలంలో సంప్రదించాలి.
చుట్టుకొలత గీతలు
అనిలాక్స్ రోల్స్ పై గీతలు పడటం అనేది అనిలాక్స్ రోల్స్ యొక్క జీవితాన్ని ప్రభావితం చేసే అత్యంత సాధారణ సమస్యలు.(చిత్రం 6)ఎందుకంటే అనిలాక్స్ రోలర్ మరియు డాక్టర్ బ్లేడ్ మధ్య ఉన్న కణాలు, ఒత్తిడి ప్రభావంతో, అనిలాక్స్ రోలర్ యొక్క ఉపరితల సిరామిక్స్ను విచ్ఛిన్నం చేస్తాయి మరియు ప్రింటింగ్ నడుస్తున్న దిశలో అన్ని మెష్ గోడలను తెరిచి ఒక గాడిని ఏర్పరుస్తాయి. ప్రింట్లోని పనితీరు ముదురు గీతలు కనిపించడం.
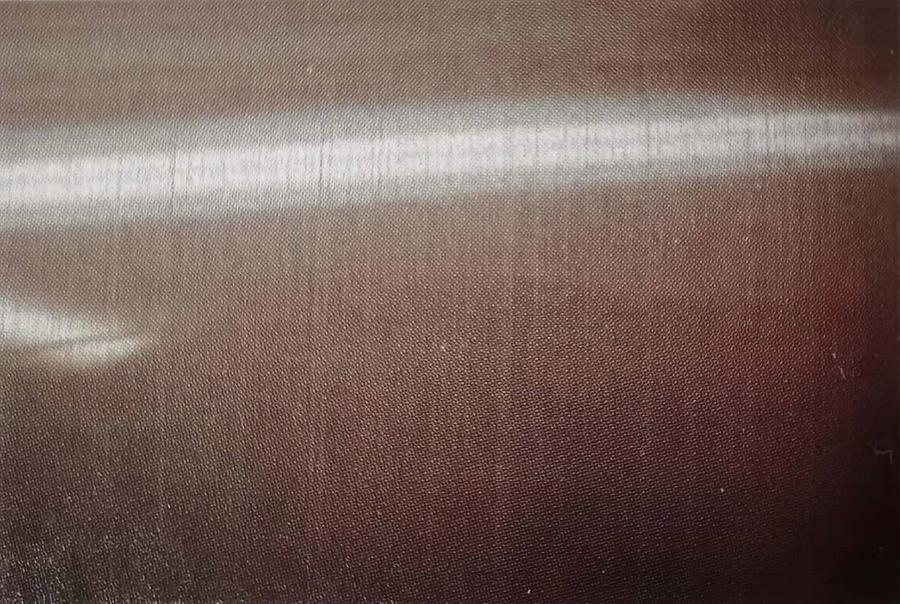
గీతలు ఉన్న అనిలాక్స్ రోల్ చిత్రం 6
గీతల యొక్క ప్రధాన సమస్య డాక్టర్ బ్లేడ్ మరియు అనిలాక్స్ రోలర్ మధ్య ఒత్తిడిలో మార్పు, తద్వారా అసలు ముఖాముఖి ఒత్తిడి స్థానిక పాయింట్-టు-ఫేస్ పీడనంగా మారుతుంది; మరియు అధిక ముద్రణ వేగం ఒత్తిడిని తీవ్రంగా పెంచుతుంది మరియు విధ్వంసక శక్తి అద్భుతమైనది. (చిత్రం 7)
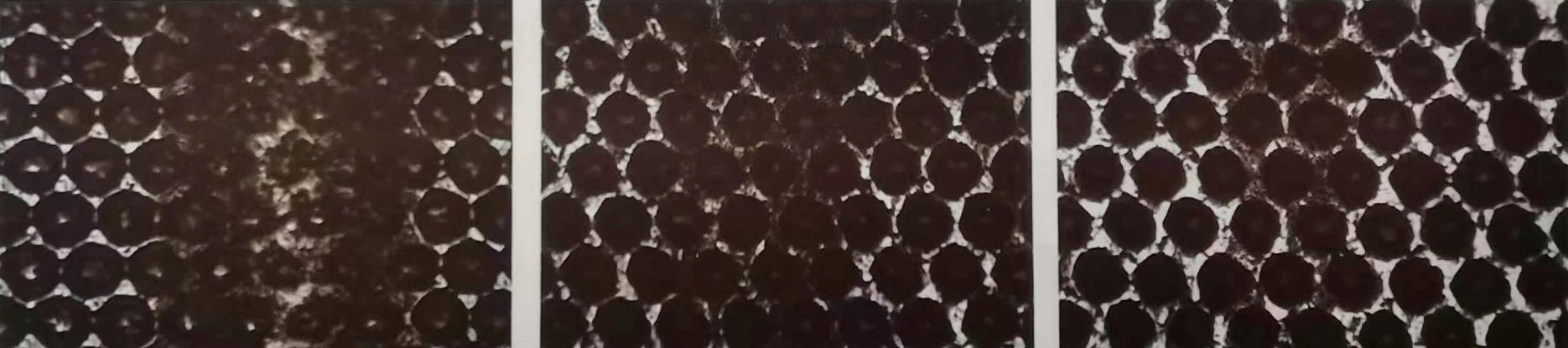
చిత్రం 7 తీవ్రమైన గీతలు
సాధారణ గీతలు
చిన్న గీతలు
సాధారణంగా, ప్రింటింగ్ వేగాన్ని బట్టి, ప్రింటింగ్ను ప్రభావితం చేసే గీతలు 3 నుండి 10 నిమిషాల్లో ఏర్పడతాయి. ఈ ఒత్తిడిని మార్చే అనేక అంశాలు ఉన్నాయి, ప్రధానంగా అనేక అంశాల నుండి: అనిలాక్స్ రోలర్ స్వయంగా, డాక్టర్ బ్లేడ్ వ్యవస్థ యొక్క శుభ్రపరచడం మరియు నిర్వహణ, డాక్టర్ బ్లేడ్ యొక్క నాణ్యత మరియు సంస్థాపన మరియు ఉపయోగం మరియు పరికరాల డిజైన్ లోపాలు.
1. అనిలాక్స్ రోలర్ కూడా
(1) సిరామిక్ అనిలాక్స్ రోలర్ యొక్క ఉపరితల చికిత్స చెక్కిన తర్వాత సరిపోదు, మరియు ఉపరితలం గరుకుగా ఉంటుంది మరియు స్క్రాపర్ మరియు స్క్రాపర్ బ్లేడ్ను సులభంగా గీసుకోవచ్చు.
అనిలాక్స్ రోలర్తో కాంటాక్ట్ ఉపరితలం మారిపోయింది, ఒత్తిడిని పెంచుతుంది, ఒత్తిడిని గుణిస్తుంది మరియు హై-స్పీడ్ ఆపరేషన్ స్థితిలో మెష్ను విచ్ఛిన్నం చేస్తుంది.
ఎంబోస్డ్ రోలర్ యొక్క ఉపరితలం గీతలు ఏర్పరుస్తుంది.
(2) పాలిషింగ్ మరియు ఫైన్ గ్రైండింగ్ ప్రక్రియలో లోతైన పాలిషింగ్ లైన్ ఏర్పడుతుంది. అనిలాక్స్ రోల్ డెలివరీ చేయబడినప్పుడు ఈ పరిస్థితి సాధారణంగా ఉంటుంది మరియు తేలికగా పాలిష్ చేయబడిన లైన్ ప్రింటింగ్ను ప్రభావితం చేయదు. ఈ సందర్భంలో, ప్రింటింగ్ ధృవీకరణను యంత్రంపై నిర్వహించాలి.
2. డాక్టర్ బ్లేడ్ వ్యవస్థ శుభ్రపరచడం మరియు నిర్వహణ
(1) చాంబర్ డాక్టర్ బ్లేడ్ స్థాయి సరిదిద్దబడినా, పేలవమైన స్థాయి ఉన్న చాంబర్ డాక్టర్ బ్లేడ్ అసమాన ఒత్తిడిని కలిగిస్తుంది. (చిత్రం 8)
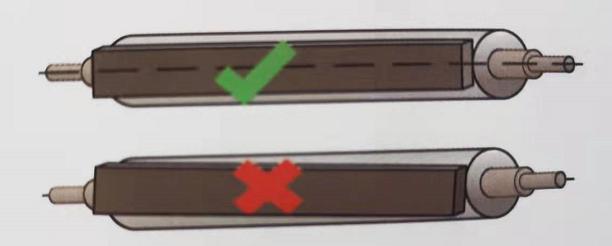
చిత్రం 8
(2) డాక్టర్ బ్లేడ్ చాంబర్ నిలువుగా ఉంచినా, నిలువుగా లేని ఇంక్ చాంబర్ బ్లేడ్ యొక్క కాంటాక్ట్ ఉపరితలాన్ని పెంచుతుంది. నిజంగా, ఇది అనిలాక్స్ రోలర్కు నేరుగా నష్టం కలిగిస్తుంది. చిత్రం 9
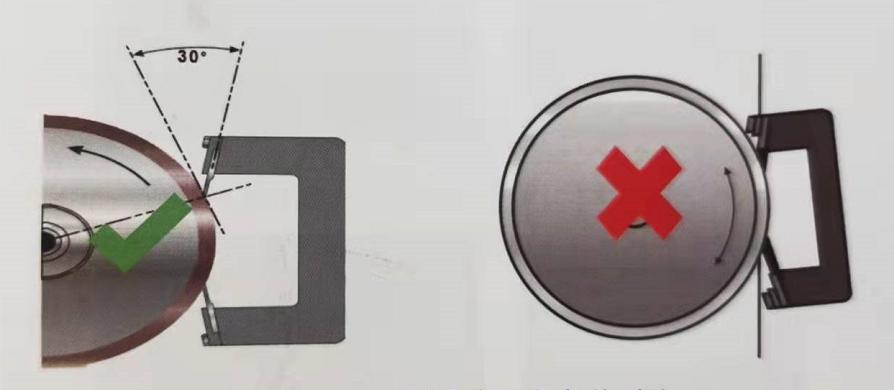
చిత్రం 9
(3) చాంబర్ డాక్టర్ బ్లేడ్ సిస్టమ్ శుభ్రపరచడం చాలా ముఖ్యం, డాక్టర్ బ్లేడ్ మరియు అనిలాక్స్ రోలర్ మధ్య చిక్కుకున్న మలినాలు ఇంక్ సిస్టమ్లోకి ప్రవేశించకుండా నిరోధించండి. ఫలితంగా ఒత్తిడిలో మార్పులు వస్తాయి. డ్రై ఇంక్ కూడా చాలా ప్రమాదకరం.
3. డాక్టర్ బ్లేడ్ యొక్క సంస్థాపన మరియు ఉపయోగం
(1) బ్లేడ్ దెబ్బతినకుండా, బ్లేడ్ తరంగాలు లేకుండా నిటారుగా ఉండేలా మరియు బ్లేడ్ హోల్డర్తో సరిగ్గా కలిపి ఉండేలా చాంబర్ డాక్టర్ బ్లేడ్ను సరిగ్గా ఇన్స్టాల్ చేయండి, ఉదా.
చిత్రం 10లో చూపిన విధంగా, అనిలాక్స్ రోలర్ ఉపరితలంపై ఒత్తిడి సమానంగా ఉండేలా చూసుకోండి.
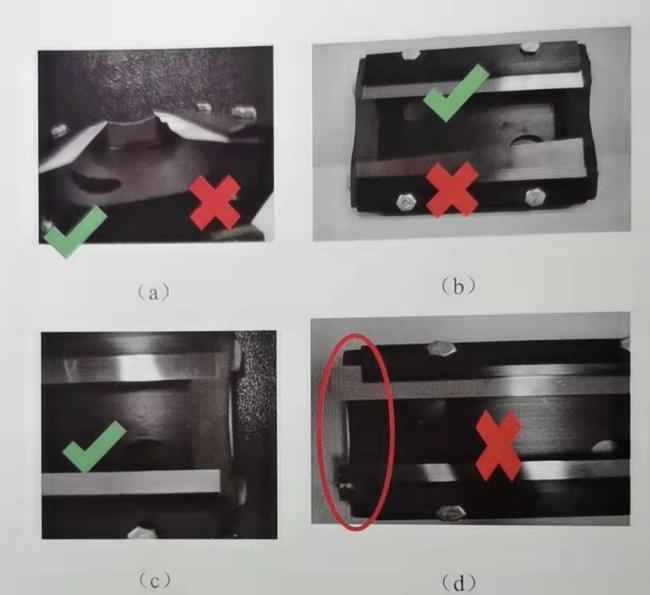
చిత్రం 10
(2) అధిక-నాణ్యత స్క్రాపర్లను ఉపయోగించండి. అధిక-నాణ్యత స్క్రాపర్ స్టీల్ గట్టి పరమాణు నిర్మాణాన్ని కలిగి ఉంటుంది, చిత్రం 11 (a)లో చూపిన విధంగా, ధరించిన తర్వాత కణాలు చిన్నవిగా మరియు ఏకరీతిగా ఉంటాయి; తక్కువ-నాణ్యత గల స్క్రాపర్ స్టీల్ యొక్క పరమాణు నిర్మాణం తగినంత గట్టిగా ఉండదు మరియు ధరించిన తర్వాత కణాలు పెద్దవిగా ఉంటాయి, చూపిన చిత్రం 11 (b)లో చూపిన విధంగా.
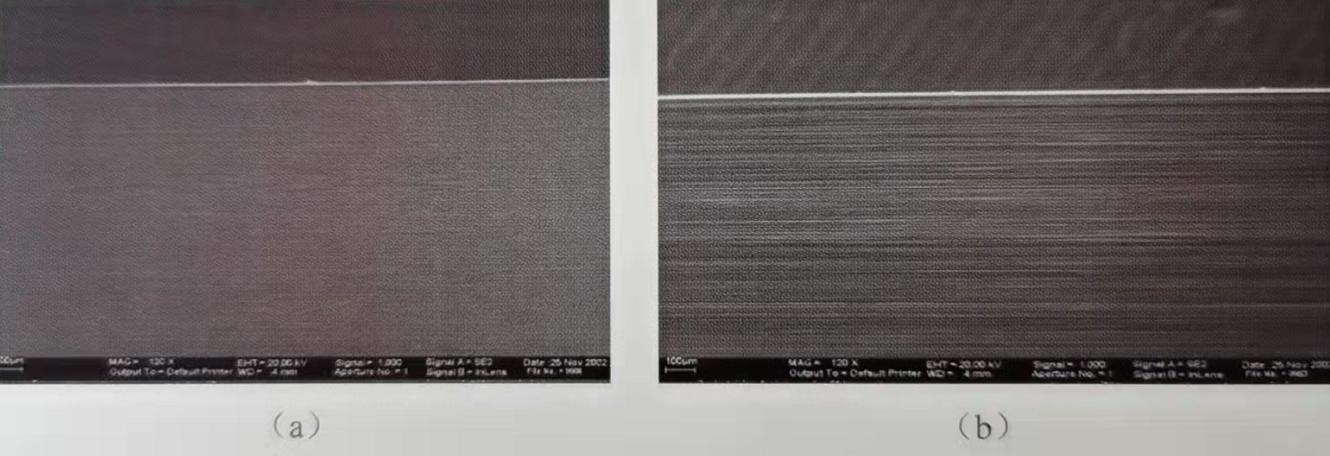
చిత్రం 11
(3) బ్లేడ్ కత్తిని సకాలంలో మార్చండి. భర్తీ చేసేటప్పుడు, కత్తి అంచు బంప్ కాకుండా రక్షించడానికి శ్రద్ధ వహించండి. అనిలాక్స్ రోలర్ యొక్క వేరే లైన్ నంబర్ను మార్చేటప్పుడు, మీరు బ్లేడ్ కత్తిని భర్తీ చేయాలి. వేర్వేరు లైన్ నంబర్లతో అనిలాక్స్ రోలర్ యొక్క వేర్ డిగ్రీ అస్థిరంగా ఉంటుంది, చిత్రం 12లో చూపిన విధంగా, ఎడమ చిత్రం తక్కువ లైన్ నంబర్ స్క్రీన్ బ్లేడ్ కత్తిపై బ్లేడ్ కత్తిని గ్రైండింగ్ దెబ్బతిన్న ఎండ్ ఫేస్ యొక్క పరిస్థితి, కుడి వైపున ఉన్న చిత్రం బ్లేడ్ కత్తికి హై లైన్ కౌంట్ అనిలాక్స్ రోలర్ యొక్క అరిగిపోయిన ఎండ్ ఫేస్ యొక్క స్థితిని చూపుతుంది. డాక్టర్ బ్లేడ్ మరియు అనిలాక్స్ రోలర్ మధ్య కాంటాక్ట్ ఉపరితలం సరిపోలని దుస్తులు స్థాయిలతో మారుతుంది, దీని వలన ఒత్తిడి మార్పులు మరియు గీతలు ఏర్పడతాయి.
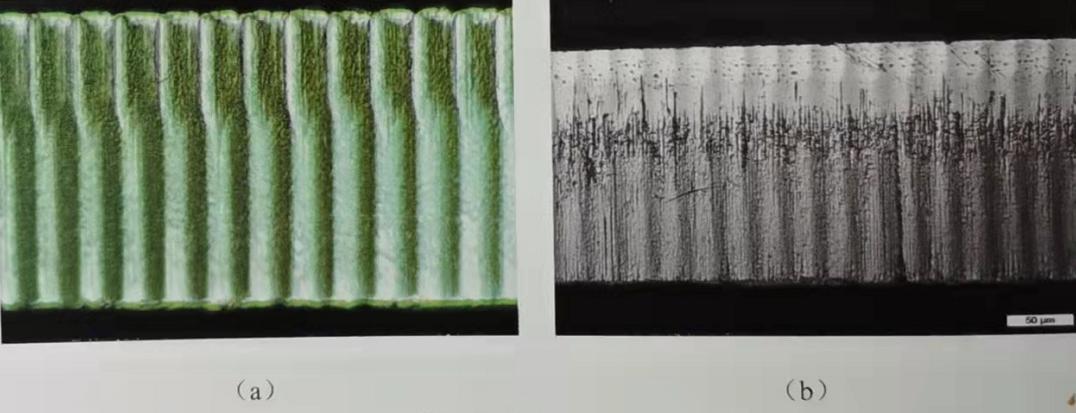
చిత్రం 12
(4) స్క్వీజీ యొక్క పీడనం తేలికగా ఉండాలి మరియు స్క్వీజీ యొక్క అధిక పీడనం స్క్వీజీ మరియు అనిలాక్స్ రోలర్ యొక్క కాంటాక్ట్ ఏరియా మరియు కోణాన్ని మారుస్తుంది, చిత్రం 13లో చూపిన విధంగా. మలినాలను చొప్పించడం సులభం, మరియు ప్రవేశించిన మలినాలు ఒత్తిడిని మార్చిన తర్వాత గీతలు ఏర్పడతాయి. అసమంజసమైన ఒత్తిడిని ఉపయోగించినప్పుడు, భర్తీ చేయబడిన స్క్రాపర్ యొక్క క్రాస్ సెక్షన్పై ధరించిన మెటల్ టెయిల్స్ ఉంటాయి. చిత్రం 14. అది పడిపోయిన తర్వాత, అది స్క్రాపర్ మరియు అనిలాక్స్ రోలర్ మధ్య చిక్కుకుంటుంది, ఇది అనిలాక్స్ రోలర్పై గీతలు ఏర్పడవచ్చు.
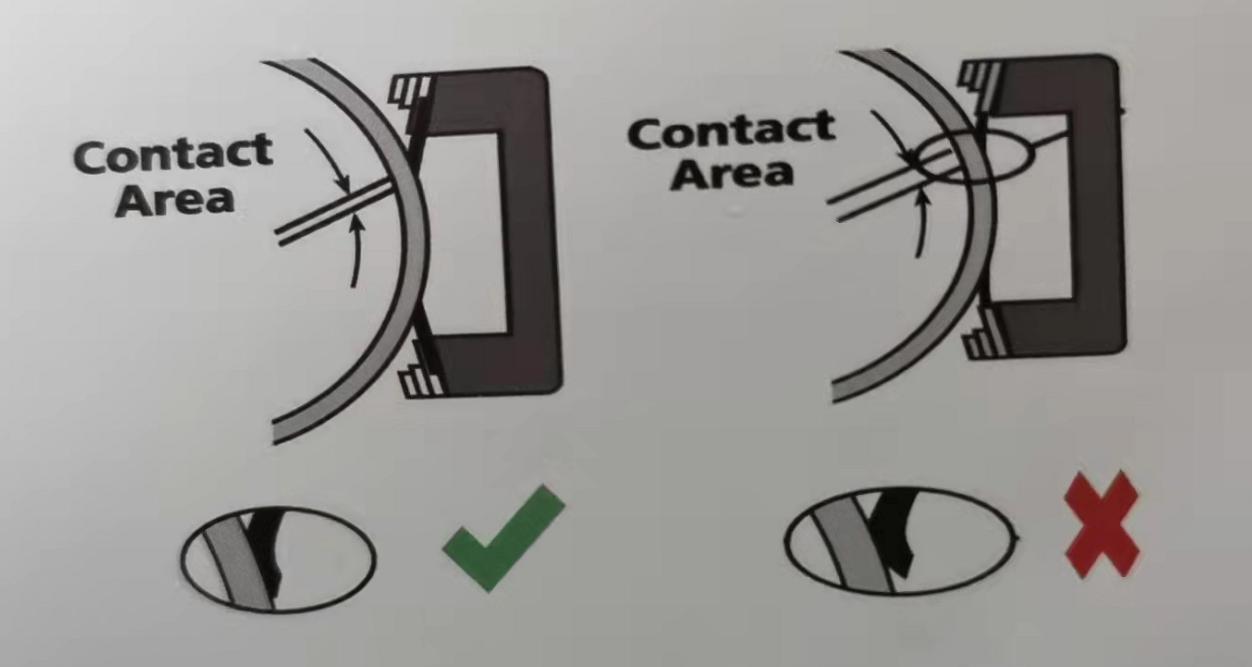
చిత్రం 13
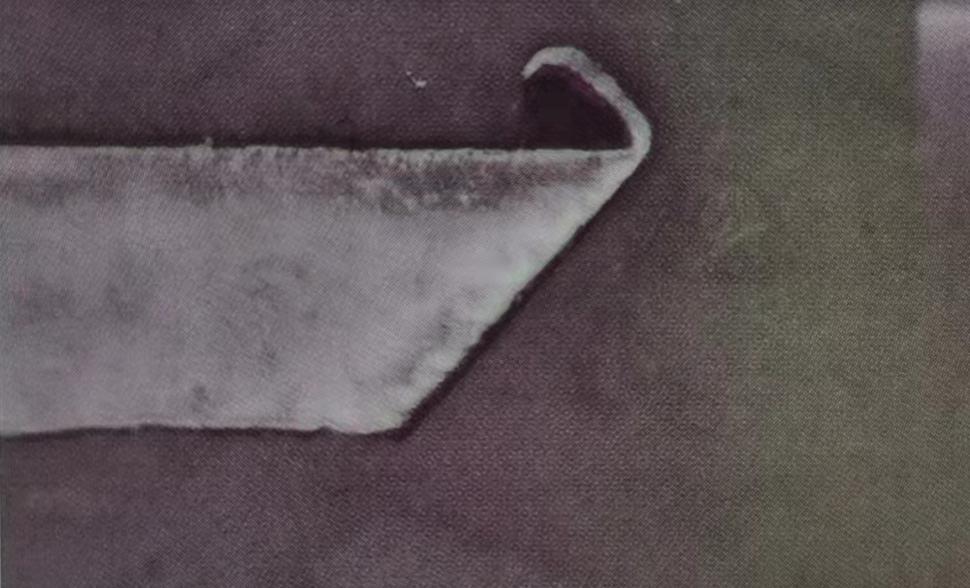
చిత్రం 14
4. పరికరాల డిజైన్ లోపాలు
డిజైన్ లోపాలు కూడా సులభంగా గీతలు ఏర్పడటానికి కారణమవుతాయి, ఉదాహరణకు ఇంక్ బ్లాక్ డిజైన్ మరియు అనిలాక్స్ రోల్ యొక్క వ్యాసం మధ్య అసమతుల్యత. స్క్వీజీ కోణం యొక్క అసమంజసమైన డిజైన్, అనిలాక్స్ రోలర్ యొక్క వ్యాసం మరియు పొడవు మధ్య అసమతుల్యత మొదలైనవి అనిశ్చిత అంశాలను తెస్తాయి. అనిలాక్స్ రోల్ యొక్క చుట్టుకొలత దిశలో గీతల సమస్య చాలా క్లిష్టంగా ఉందని చూడవచ్చు. ఒత్తిడిలో మార్పులు, సమయానికి శుభ్రపరచడం మరియు నిర్వహణ, సరైన స్క్రాపర్ను ఎంచుకోవడం మరియు మంచి మరియు క్రమబద్ధమైన ఆపరేటింగ్ అలవాట్లపై శ్రద్ధ చూపడం వల్ల స్క్రాచ్ సమస్య చాలా వరకు తగ్గుతుంది.
ఢీకొనడం
సిరామిక్స్ యొక్క కాఠిన్యం ఎక్కువగా ఉన్నప్పటికీ, అవి పెళుసుగా ఉండే పదార్థాలు. బాహ్య శక్తి ప్రభావంతో, సిరామిక్స్ సులభంగా పడిపోతాయి మరియు గుంటలు ఏర్పడతాయి (చిత్రం 15). సాధారణంగా, అనిలాక్స్ రోలర్లను లోడ్ చేసేటప్పుడు మరియు అన్లోడ్ చేసేటప్పుడు లేదా మెటల్ ఉపకరణాలు రోలర్ ఉపరితలం నుండి పడిపోతున్నప్పుడు గడ్డలు ఏర్పడతాయి. ప్రింటింగ్ వాతావరణాన్ని శుభ్రంగా ఉంచడానికి ప్రయత్నించండి మరియు ప్రింటింగ్ ప్రెస్ చుట్టూ, ముఖ్యంగా ఇంక్ ట్రే మరియు అనిలాక్స్ రోలర్ దగ్గర చిన్న భాగాలను పేర్చకుండా ఉండండి. అనిలాక్స్తో మంచి పని చేయాలని సిఫార్సు చేయబడింది. చిన్న వస్తువులు పడిపోకుండా మరియు అనిలాక్స్ రోలర్తో ఢీకొనకుండా నిరోధించడానికి రోలర్ యొక్క సరైన రక్షణ. అనిలాక్స్ రోలర్ను లోడ్ చేసేటప్పుడు మరియు అన్లోడ్ చేసేటప్పుడు, ఆపరేషన్కు ముందు దానిని ఫ్లెక్సిబుల్ ప్రొటెక్టివ్ కవర్తో చుట్టాలని సిఫార్సు చేయబడింది.
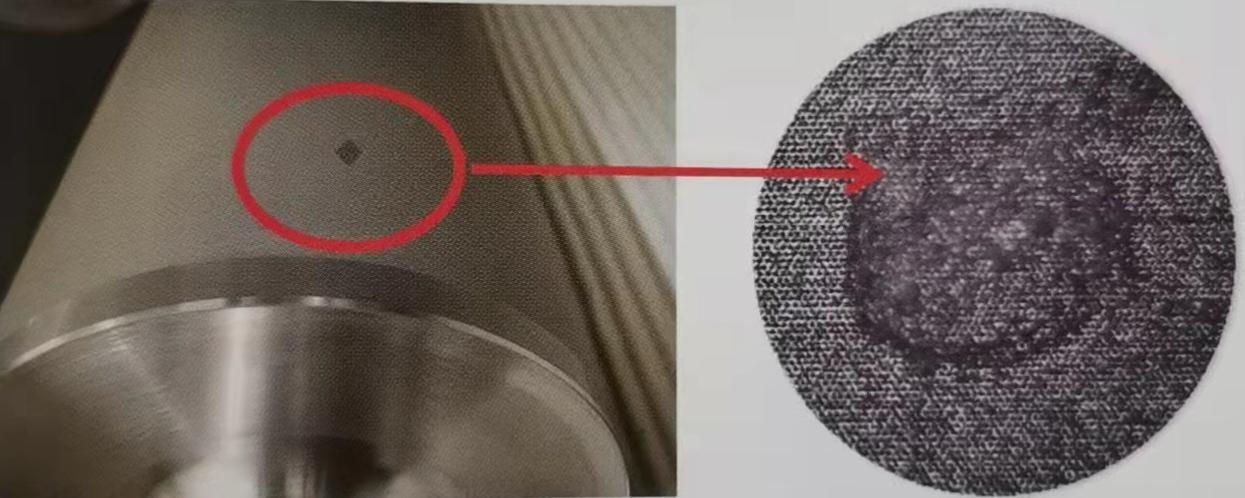
చిత్రం 15
పోస్ట్ సమయం: ఫిబ్రవరి-23-2022